Silk screening is an old printing technique that utilizes a stencil and allows the dye to get deposited on a fabric like silk, cotton, etc., by rubbing or spraying the ink. The screen printing technique was initially used to print different types of fabrics, but now the method has evolved. Hence it allows printing on a variety of surfaces, especially plastics like polyester.
Since many designs can be customized using the silk screen method, many brands are using this method for promoting and designing their products. The silk screening technique is also cost-effective for getting bright and vibrant prints. Thus, if someone wants a silk-screener for their products, they can look up online in order to get such services.
The Details Of The Technique
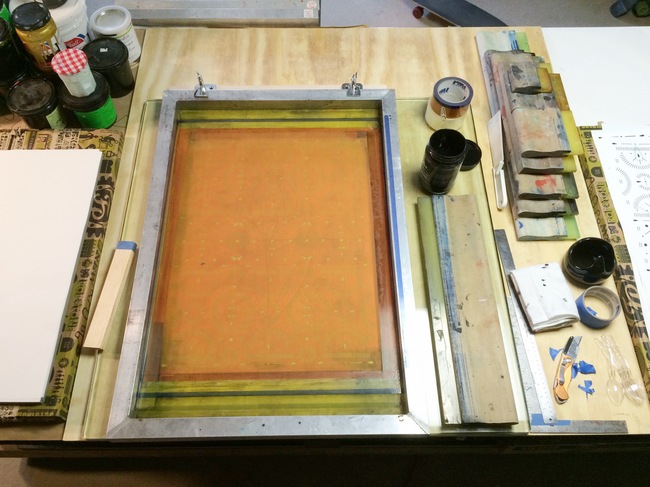
The process of printing involves a screen made of fabric or plastics like polyester. The screen is coated with a photosensitive dye. The dye coating step is highly light-sensitive and is carried out in the absence of light in a dark room. The screen is then burnt in such a manner that the design or the stencil through which the dye needs to seep in gets cut out in the screen.
After this, an appropriate dye is selected, which is deposited on the printing surface through the screen. Once the design gets imprinted on the surface, it is bonded permanently to the surface using high temperature (curing).
What Makes The Process Hard?
The Choice Of Ink
Several types of inks can be used for printing, like discharge inks, plastisols etc. Discharge inks are water-based dyes where the ink discharges the original color of the fabric on which the imprinting is to occur. Apart from this, there are specific dyes that are to be used to create three-dimensional images or complex color patterns. The choice of dye is crucial in deciding the quality of the final outcome.
The choice of ink depends on a number of factors, like the type of image required, its color, and texture. It also varies with the surface on which the imprinting has to happen. They are different for metallic, ceramic, plastic, and textile-based surfaces. If someone uses water-based ink for the light color background, it will sit well.
However, for dark backgrounds, discharge ink is the best option. Thus, success in this printing process requires a lot of background knowledge about different surfaces and their most compatible ink types.
Creating A Proper Contact Surface
The amount of dye that is deposited on a surface depends on the contact that is established between the screen and the surface. If the contact does not happen for the right duration, then the final product will suffer. For instance, if the duration of the contact is longer, then some adhesive dyes might get too strongly attached to the surface.
Poor Quality Of Print
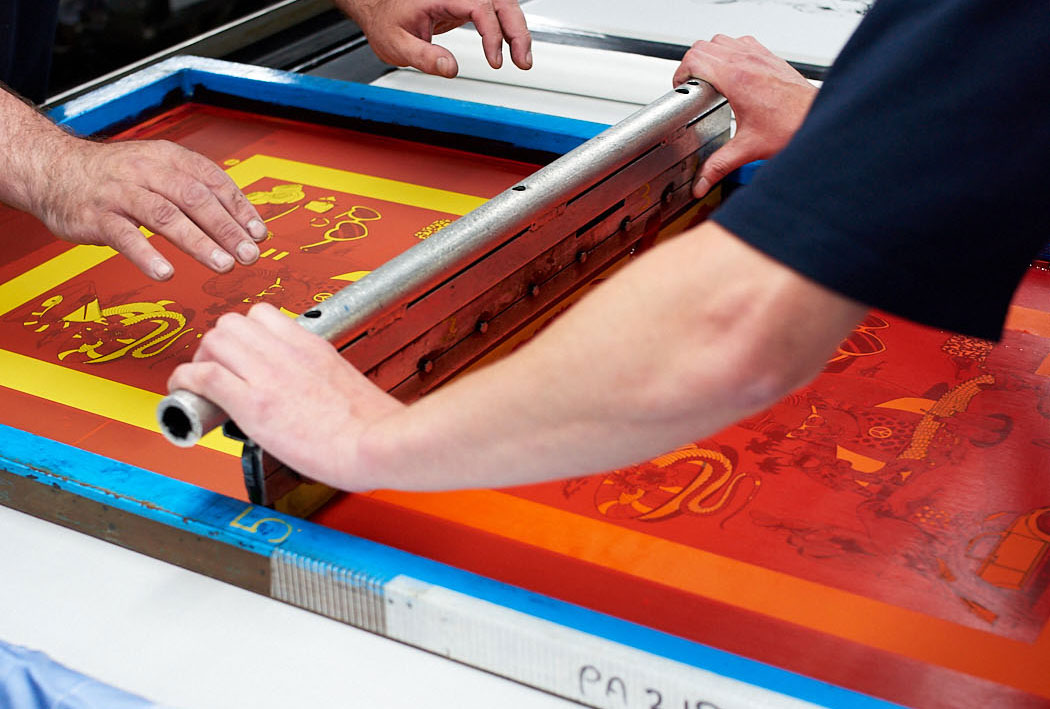
The quality of the print is considered poor if the color fades away easily after a wash or two or if the print is so light that there is a bleed-through of the background color. Sometimes the ink may even appear cracked after the printing is over.
If the color washes away after a few washes, it might be a problem with the curing process.
Tight bonds between the surface and dye form only at the appropriate temperature; hence if the temperature is less than what is optimum, the dye will wash away.
Hence it is prudent to check the temperature during the curing process and increase it to the requisite temperature to get the best results possible. Monitoring the curing temperature can also prevent cracking of the design. In order to check if the design will eventually crack or not, just pulling the printed fabric can be a quick test quality check.
Other significant problems include sticky imprints. The designs may be so sticky that they stick to the packing boxes. The major problem, in this case, is usually not giving enough time for the print to cool down after the high temperature-based binding step. Thus, there are multiple things that can go wrong to result in a poor-quality image.
Problems Of Roughness And Fibrillation
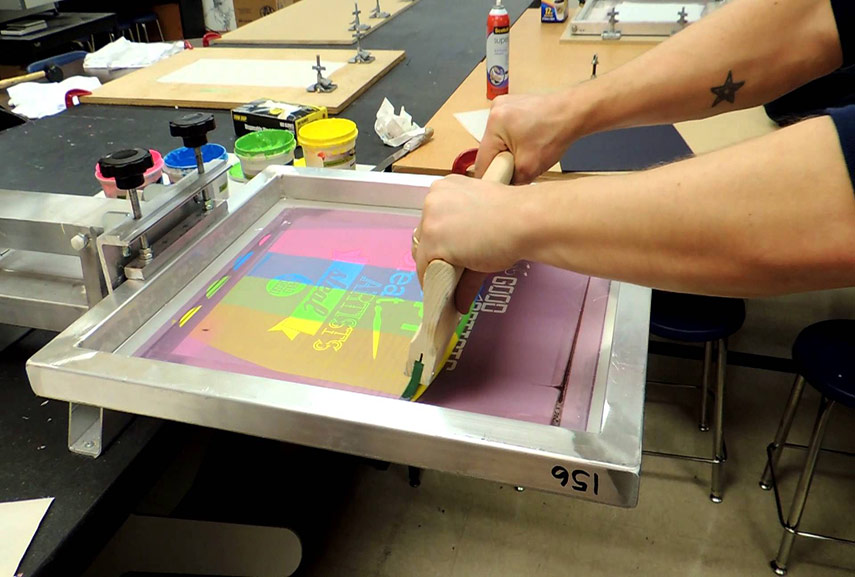
The end product might feel stiff or fibrillated. Plastisol dyes usually give a hard feel when touched. Adding a softener can reduce the problem of roughness to a great extent. Fibrillation of the surface happens due to the poor quality of the substrate (material on which the printing happens).
If the substrate fibrillates, then the print appears faded or fuzzy. Using a substrate that has more strength and integrity can help. Also, using a thicker layer of ink can reduce the fuzzy feel of the final product to a great extent.
Substrate Color Interfering With Ink Color
When the substrate is dark colored, then heat might cause the dark color from the substrate to undergo sublimation( changing into a vapor state directly from a solid state) and get deposited on the printed ink, thus distorting the overall design and color.
A way to avoid this problem is curing that is done at a lower temperature and for a longer duration.
Conclusion
Silkscreen is a straightforward, affordable, and ancient printing method that has gained wide popularity. The method has become quite popular because of its ability to use a wide range of substances and create bright and colorful designs. Despite being a popular technique, it is not easy to master.
There are multiple things that can go wrong at each of the steps. The problems increase further as newer forms of inks and printing surfaces are being used in the industry. Since each ink or substrate has some specific conditions under which it works best, the technique becomes very complicated for a newcomer to master.
Since multiple steps can go wrong in silk screening, troubleshooting is also not easy. Also, there is no particular ink or substrate that is perfect. For instance, plastisol inks are vibrant but form a slurry quickly. Hence getting an ideal silk screen is quite a tough job.